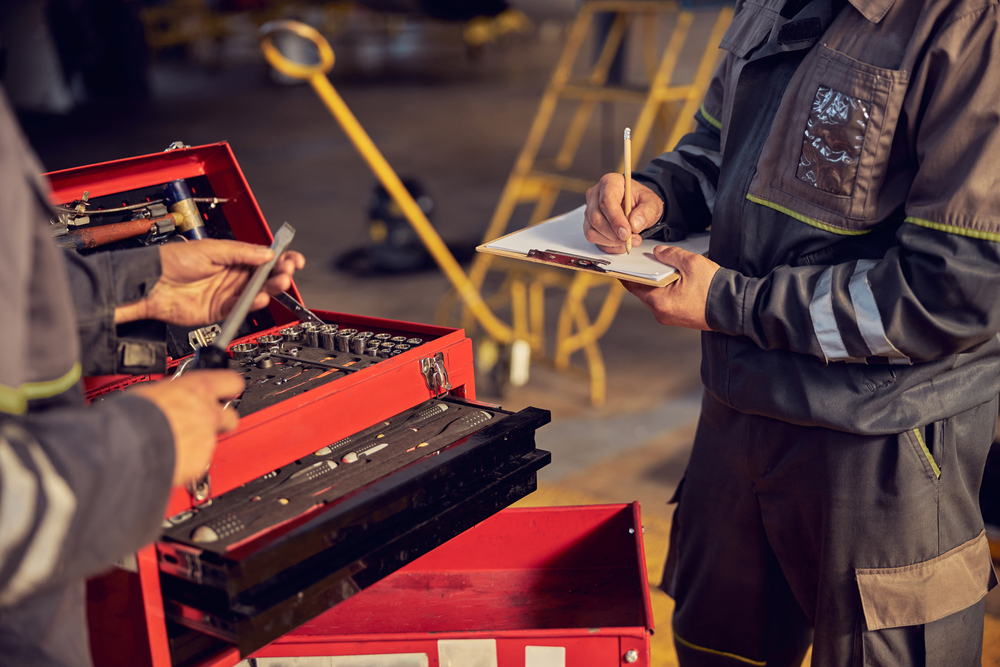
Supplying aircraft parts is a complex and highly regulated industry. Ensuring the availability, quality, and compliance of these parts is essential to maintaining the safety and efficiency of aircraft operations. This blog will explore the common challenges faced by aircraft parts suppliers and highlight the importance of quality control in aircraft parts.
Quality Control in Aircraft Parts
One of the most significant challenges for aircraft parts suppliers is maintaining rigorous quality control. Ensuring that every part meets stringent industry standards and regulations is crucial for the safety and reliability of aircraft. Here’s a closer look at the various aspects of quality control in aircraft parts.
Stringent Industry Standards
The aviation industry is governed by numerous standards and regulations to ensure the safety and reliability of aircraft. These include standards set by organizations such as:
- Federal Aviation Administration (FAA)
- European Union Aviation Safety Agency (EASA)
- International Air Transport Association (IATA)
Suppliers must comply with these regulations, which often involve rigorous testing and certification processes.
Traceability and Documentation
Another critical aspect of quality control is maintaining traceability and comprehensive documentation for each part. This ensures that the entire history of a part, from manufacturing to installation, is recorded and accessible. This level of traceability helps in identifying and addressing any potential issues promptly.
Counterfeit Parts Detection
The influx of counterfeit parts is a growing concern in the aviation industry. These parts can pose significant safety risks if installed in aircraft. Suppliers must implement robust measures to detect and prevent the distribution of counterfeit parts. This involves:
- Thorough inspections
- Verification processes
- Collaboration with trusted manufacturers and distributors
Inventory Management
Effective inventory management is another challenge faced by aircraft parts suppliers. Balancing the availability of parts with the costs of maintaining inventory requires careful planning and forecasting.
Demand Forecasting
Accurately predicting the demand for aircraft parts is crucial for maintaining optimal inventory levels. This involves analyzing:
- Historical data
- Industry trends
- Operational needs of airlines and maintenance organizations
Inaccurate forecasting can lead to either excess inventory, resulting in higher holding costs, or stockouts, causing delays in aircraft maintenance and operations.
Lead Time Management
The lead time for manufacturing and delivering aircraft parts can be lengthy, especially for specialized or custom parts. Suppliers must manage these lead times effectively to ensure timely delivery and avoid disruptions in the supply chain. This requires:
- Strong relationships with manufacturers
- A well-coordinated logistics strategy
Regulatory Compliance
Aircraft parts suppliers must navigate a complex landscape of regulatory requirements. Compliance with these regulations is essential to avoid penalties, maintain certifications, and ensure the safety and reliability of aircraft.
Certification and Audits
Suppliers need to obtain and maintain various certifications, such as AS9100 (a widely adopted quality management system for the aerospace industry) and other relevant standards. Regular audits by regulatory bodies and customers ensure that suppliers adhere to these standards. Preparing for and passing these audits requires:
- Continuous improvement
- Adherence to best practices
Environmental Regulations
Environmental regulations are becoming increasingly stringent in the aerospace industry. Suppliers must ensure that their processes and products comply with environmental standards, such as those related to:
- Hazardous materials
- Waste management
This involves adopting sustainable practices and materials wherever possible.
Technological Advancements
The rapid pace of technological advancements in the aviation industry presents both opportunities and challenges for aircraft parts suppliers. Keeping up with these changes is essential to remain competitive and meet the evolving needs of customers.
Adoption of New Technologies
Suppliers must invest in new technologies to improve the efficiency and quality of their operations. These technologies can enhance production processes, reduce lead times, and improve the accuracy of parts. Key technologies include:
- Advanced manufacturing techniques (e.g., 3D printing)
- Digital twins
- IoT (Internet of Things) solutions
Cybersecurity
With the increasing digitization of the supply chain, cybersecurity has become a critical concern. Suppliers must protect their systems and data from cyber threats to ensure the integrity and security of their operations. This involves:
- Implementing robust cybersecurity measures
- Staying updated with the latest security protocols
Supply Chain Disruptions
Supply chain disruptions can have significant impacts on the availability and delivery of aircraft parts. Suppliers must develop strategies to mitigate these risks and ensure a resilient supply chain.
Global Events and Geopolitical Risks
Global events, such as natural disasters, pandemics, and geopolitical tensions, can disrupt the supply chain and affect the availability of parts. Suppliers need to develop contingency plans and diversify their supply base to minimize the impact of these disruptions.
Supplier Relationships
Building and maintaining strong relationships with suppliers and manufacturers is crucial for ensuring the timely delivery of parts. Suppliers must:
- Establish clear communication channels
- Negotiate favorable terms
- Collaborate closely with their partners to address any issues that arise
Conclusion
The challenges faced by aircraft parts suppliers are multifaceted and require a proactive approach to overcome. Ensuring quality control in aircraft parts is paramount to maintaining the safety and reliability of aircraft. By addressing issues related to inventory management, regulatory compliance, technological advancements, and supply chain disruptions, suppliers can better meet the needs of the aviation industry and contribute to its continued growth and safety.
Need a Fixed-Base Operator in Dayton, OH?
Ensuring the highest standards in aircraft parts supply is no small feat, but here at First Flight Aviation, we rise to the challenge every day. We understand the critical importance of quality control, regulatory compliance, and efficient inventory management. Whether you’re looking for reliable parts or need guidance navigating the complexities of the aviation supply chain, our expert team is here to help. Reach out to us today to learn how we can support your operations and keep your aircraft flying safely and efficiently. Let’s soar together with confidence and precision!